Né dans les années 50 dans les usines japonaises de Toyota, le Lean a su s'imposer comme approche allégée et bienveillante de gestion de production visant à réduire les gaspillages tout en garantissant l'amélioration continue.
Initialement conçu pour l’industrie, le Lean s’adapte parfaitement à de nombreux domaines – on parlera par exemple de Lean Management, de Lean Startup ou encore de Lean IT en fonction du domaine d’application – et des cadres de travail plus récents comme Scrum (issu de l’Agilité, un autre mouvement qui a su naître en parallèle du Lean) se rattachent désormais directement et explicitement au Lean. Cette ouverture à de nouveaux horizons permet d’envisager de nouvelles utilisations aux nombreux outils et pratiques du Lean, parmi lesquelles le Kanban, les Mudas, le Kaizen ou encore les chantiers 5S. C’est sur ces derniers (les chantiers 5S) que nous allons nous attarder dans cet article, particulièrement comment je m’en suis servi pour gérer un Product Backlog dans un contexte Scrum, mais revenons d’abord à l’origine de son utilisation dans l’industrie.
Le 5S comme outil du Lean et dans l’industrie
Le 5S est un outil du Lean principalement utilisé dans le milieu industriel, et plus particulièrement dans l’organisation des magasins et ateliers. Le 5S va permettre par exemple d’organiser les consommables (visseries, capteurs, moteurs, etc..) de façon claire pour tous.
Le Lean décrit le 5S comme une méthode d’amélioration, il vise avant tout à réduire les gaspillages, notamment en termes de temps perdu, en simplifiant tout ce qui peut l’être et en supprimant l’inutile.
Les 5 opérations du 5S
Comme beaucoup d’outils du Lean, les termes sont en japonais, le 5S consiste en 5 étapes à faire l’une après l’autre dans l’ordre suivant :
- Seiri (Ranger) : Supprimer l’inutile
- Seiton (Ordre) : Situer les choses
- Seiso (Nettoyage) : faire Scintiller
- Seiketsu (Propre) : définir des Standards
- Shitsuke (Education) : Suivre et progresser
- Seiri : la première étape consiste à identifier et supprimer l’inutile. Tout ce qui ne sert pas régulièrement doit être recyclé, jeté ou archivé. On identifiera ce qui devrait être placé au plus proche du travail du fait qu’il s’agit de ce que l’on doit utiliser en premier ou le plus régulièrement. L’objectif est d’augmenter la concentration en supprimant les distractions et les interruptions.
- Seiton : le but de cette deuxième étape est d’éviter les pertes de temps et d’énergie en classant les éléments de la façon la plus logique possible. On paraphrase souvent Seiton par « Une place pour chaque chose, et chaque chose à sa place ». On va donc regrouper les éléments similaires ensemble en les catégorisant. Le résultat de cette étape est un environnement de travail où la recherche d’un élément précis est facilitée par son organisation. On favorisera, sans que cela soit obligatoire, la gestion en FIFO (First In First Out, ou en français, premier arrivé, premier sorti, comme dans une file d’attente par exemple), et non pas en LIFO (Last In First Out, ou en français dernier arrivé premier sorti, comme pour une pile d’assiette).
- Seiso : pour cette troisième étape, on va chercher à éviter au maximum la survenue de futures anomalies en facilitant au maximum leur détection. On va donc nettoyer notre environnement de travail et décrasser/réparer ce qui doit l’être. Il s’agit du 1er pas vers l’auto-gestion et la maintenance systématisée de l’environnement de travail et de ses éléments.
- Seiketsu : cette quatrième étape est celle de la standardisation, il s’agit de définir les règles qui permettront d’éviter au maximum au désordre de venir s’installer. Il est conseillé d’utiliser au maximum le management visuel et l’étiquetage. Par exemple, dans un atelier, on donnera un coup de bombe de peinture sur l’établi afin que la forme de chaque outil soit présente, on remarquera ainsi facilement où ranger un outil et/ou si un outil est manquant.
- Shitsuke :le but de cette cinquième et dernière étape est d’éduquer toutes personnes agissant dans l’environnement de travail afin que la pratique du 5S devienne une habitude du quotidien. Pour que le 5S ne soit pas un échec (voire plus bas), il est nécessaire que chacun adhère aux règles de standardisation et de rangement que l’on aura mises en place. C’est pourquoi il est conseillé de ne pas imposer ces règles, mais de les définir avec les personnes concernées, le but étant de les maintenir dans le temps le plus longtemps possible pour éviter d’avoir à refaire à nouveau un 5S.
Équivalent en français : ORDRE
Le 5S est aussi connu sous l’acronyme français ORDRE :
- Ordonner
- Ranger
- Dépoussiérer / Découvrir des anomalies
- Rendre évident
- Être rigoureux
Le 5S appliqué à la vie de tous les jours
Et si je vous disais que vous appliquez très probablement le 5S naturellement et quotidiennement chez vous sans même vous en rendre compte ?
Vous ne voyez pas ?
Si je vous demande comment vous organisez vos denrées alimentaires ou votre vaisselle ? Par exemple, les fourchettes ont sûrement une place précise dans votre foyer, tout comme les assiettes, les verres, les couteaux, etc.. vous avez en effet identifié des espaces de rangement précis pour chacun de ces éléments, et si une cuillère se retrouve malencontreusement là où se trouve les fourchettes, vous considérez cela comme une anomalie et la corrigez vraisemblablement assez rapidement. De même, il ne vous viendrait pas à l’idée de mettre une fourchette sale parmi celles qui sont propres.
Pensez-y la prochaine fois que vous rangez votre vaisselle, regardez chaque chose que vous faites, et essayez de l’associer à chacune des étapes du 5S.
Gestion d’un Product Backlog avec le 5S
Le 5S peut tout à fait s’appliquer à la gestion d’un Backlog ou à sa réorganisation quand la gestion aura fait défaut. J’ai personnellement introduit le 5S dans ma sphère professionnelle pour atteindre cet objectif. Ma dernière utilisation a eu lieu sur un Backlog composé de plus d’une centaine d’items, pas tous définis selon la même nomenclature, avec description ou non et contenant des tâches obsolètes ou importantes… l’opération a mobilisé une bonne partie de l’équipe et a nécessité une journée entière.
Avant de mener ce genre d’opération, je vous conseille bien entendu d’insister sur le fait qu’il n’est pas du tout souhaitable de recommencer le 5S à zéro régulièrement et qu’il faut se discipliner pour maintenir le système dans un parfait état de fonctionnement. Pour cela, il est donc important de faire comprendre aux personnes concernées que ce process est coûteux et douloureux, mais devient irrémédiablement nécessaire lorsque l’on a laissé s’installer le désordre.
En bref, voici la stratégie utilisée, en cohérence avec le 5S, pour ordonner efficacement un Backlog :
- Seiri : supprimer l’inutile. On peut par exemple, même si cela peut paraître brutal, définir une date à partir de laquelle on considère que les items du Backlog sont devenus obsolètes et archiver tous les items plus vieux que cette date (par exemple plus d’un an) : les items réellement nécessaires surgiront de nouveau par le terrain et on pourra ainsi évaluer le rapport coût/bénéfice de leur prise en compte plus facilement. Pour être moins brutal, on peut également regarder chaque item un par un en ayant à sa disposition un représentant du client ou des utilisateurs, ou à défaut un membre de l’équipe parfaitement conscient du métier, mais cela peut vite devenir chronophage, c’est pourquoi je recommande de mixer ces 2 approches.
- Seiton : Situer les choses. Une fois la première étape réalisée, on passera de nouveau en revue chaque item afin, si nécessaire, de le mettre dans le bon Backlog (dans le cas où le Backlog initial fait référence à plusieurs produits), et prioriser les tâches entre elles. S’il n’y a pas de possibilité de définir facilement et rapidement une business value et/ou des points d’efforts, il est conseillé de placer les items sur lesquels on dispose du plus de connaissances en premier et à l’inverse, les items les plus vagues en dernier.
- Seiso : Faire scintiller. Vient ensuite la phase de nettoyage, le but va surtout être de faciliter la détection des anomalies et de les corriger si elles sont présentes. Personnellement, je profite de cette étape pour ajouter les quelques éléments de description qu’il pourrait manquer et réécrire si nécessaire l’item sous forme d’User Story.
- Seiketsu : Standardiser. Cela peut par exemple être fait (par un Product Owner, seul responsable du Backlog) via la mise en place d’étiquettes et de filtres, de règles d’ajout (ajout par défaut en haut ou en bas du Backlog), de règles de priorisation des items entre eux, d’un espace tampon pour tout item non prêt (attention cependant à ce que cela ne devienne pas un 2nd Backlog, il faudra donc s’assurer que la durée de vie de chaque item soit la plus courte possible dans cet espace tampon), d’une Definition of Ready ou tout autre ajustement que l’on jugera nécessaire. Attention, la standardisation doit rester simple afin que son adhésion soit également la plus simple possible.
- Shitsuke : éduquer. Pour la dernière étape, la plus importante selon moi, il est nécessaire d’expliquer le fonctionnement du Backlog à toute personne ayant besoin de le visualiser (membres de l’équipe, mais aussi managers et décisionnaires par exemple). Le mieux est de partir du constat d’échec et de construire les règles de standardisation avec les personnes concernées pour enfin en arriver à une proposition concrète de fonctionnement (en s’appuyant par exemple sur le management visuel, qui permet de rendre les règles de gestion compréhensibles en un coup d‘oeil, voire sur l’automatisation pour ne même plus avoir à y penser). Cette proposition n’est pas à graver dans le marbre, il faut bien entendu favoriser l’amélioration continue, mais il faut rester vigilant sur l’application stricte du 5S et donc des règles qui ont été décidées conjointement quitte à les faire évoluer au fur et à mesure des retours d’expériences afin d’éviter toute dérive qui conduirait à l’échec de l’utilisation du 5S.
Pourquoi le 5S ne fonctionne pas ?
Il arrive assez souvent que l’application du 5S ne dure qu’un temps et que l’on retrouve notre bon vieux désordre, le chaos appelant le chaos, il ne suffit que d’une petite exception à la règle pour voir le travail du 5S anéantit en quelques instants. C’est le cas de la petite User Story non rangée comme il faut dans le Backlog, parce qu’on le fera « plus tard »… et qui malheureusement ne le sera jamais (rangée) car, comme la loi de Leblanc le stipule, “plus tard” veut dire … “jamais”.
Cela arrive le plus souvent du fait que le 5S n’a pas été mené jusqu’à son terme. Suite à la standardisation de la 4ème étape (Seiketsu), beaucoup s’arrêteront là en se disant qu’ils ont enfin un Backlog ou un atelier bien rangé, pratique à utiliser, ignorant l’étape qui, à mon sens, est la plus importante : Shitsuke, pour éduquer sur les pratiques. Parce qu’on néglige cette étape, pour des raisons de contrainte budgétaire ou parce qu’on ne la juge pas nécessaire, on favorise le retour inexorable du désordre (une User Story non rangée dans le Backlog, puis une 2ème puisque de toute façon il y en avait une 1ère, etc..). A noter concernant le Backlog (pour faire l’analogie avec les frameworks Agile) : Scrum nécessite d’avoir un Product Owner, ce qui facilite grandement la dernière étape du 5S, la plus difficile, puisque le Product Owner est le seul à agir sur le Backlog et donc le garant de l’application du 5S. Rappelons-nous cependant, que Scrum nécessite que la communication du contenu du Product Backlog soit suffisamment claire pour l’ensemble des intéressés (équipe Scrum, mais aussi parties prenantes), il sera donc pertinent que, même si le Product Owner est seul responsable de la gestion du Product Backlog, la standardisation de celui-ci soit tout de même issue d’une réflexion favorisant l’intelligence collective.
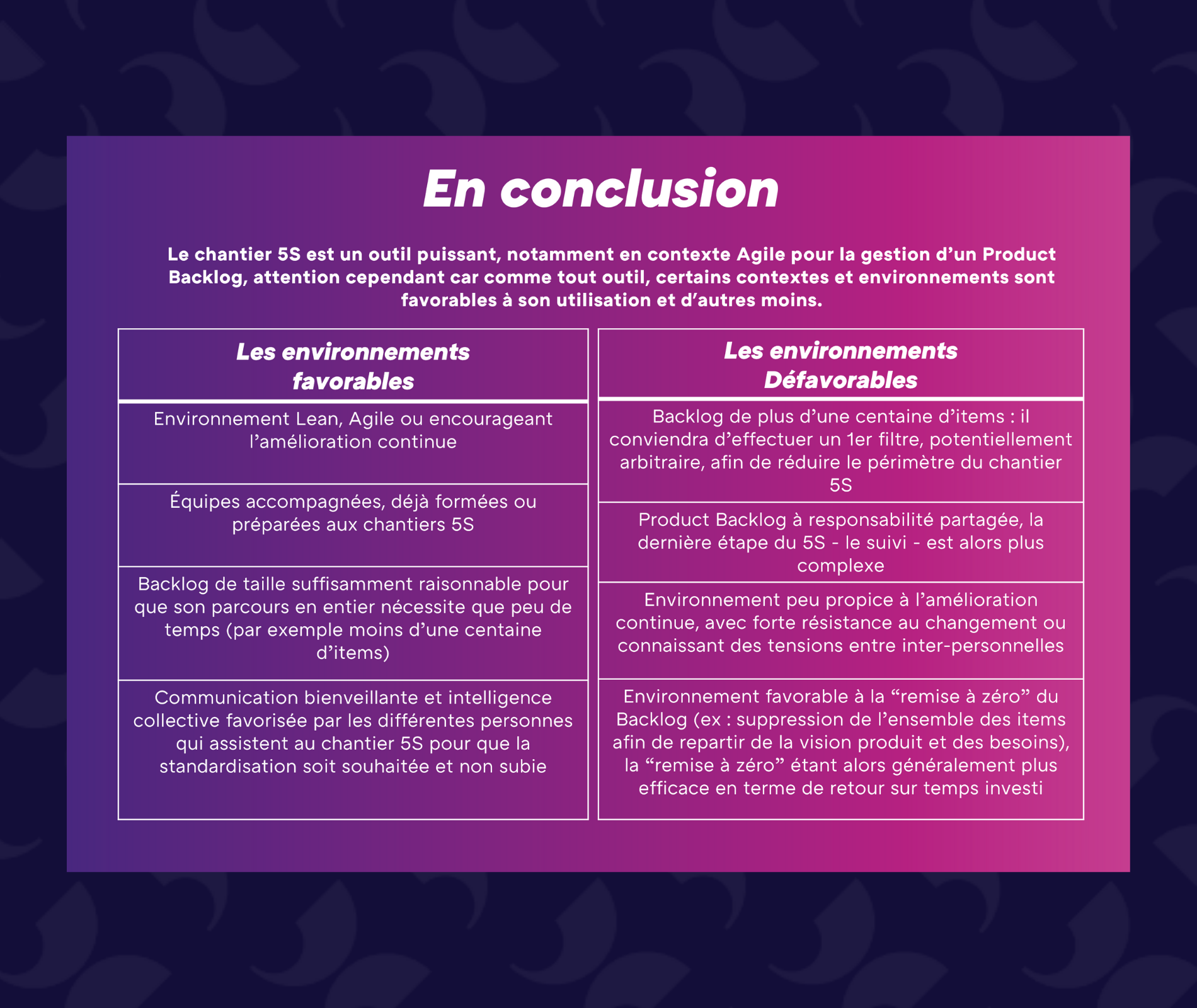